Your cart is currently empty!
Considerations in complete kitchen replacement
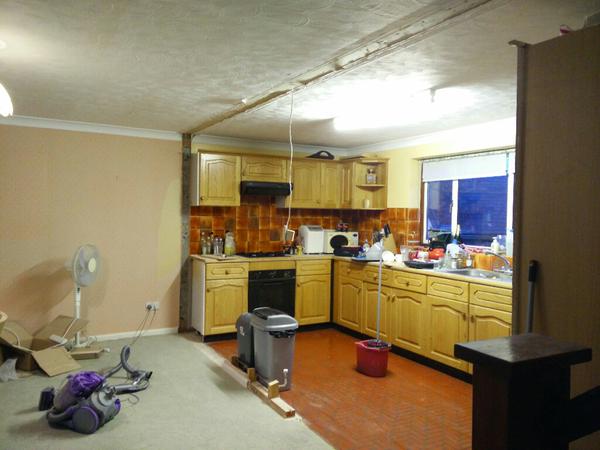
I’ve had a busy few weeks, and I’m currently in the middle of probably the largest house project I’ve undertaken. In my last post I talked about removing the wall that used to be between the dining room and kitchen. This was the precursor to removing the old kitchen and installing a new one.
In the last week I have completed removal of the old kitchen, so I now have a large empty room, and it is time to start putting things back together.
I thought I would write some notes on the various considerations that I’ve had to make to get me this far, and some of the next steps. I’m doing almost all of the work myself, but there are some things that I am outsourcing and those things require coordination.
Things I need other people for
Electrics, whilst I’m pretty confident in my ability to handle wiring jobs, the reality is that the building regulations require me to either make use of a qualified professional, or pay a fee to have one sign off on anything I do. I decided I might just as well hire an electrician. I needed them to relocate a light switch (it used to sit on the wall I removed) and run all the wiring for new spotlights for the kitchen, removing the old florescent tube. The electrician needed to drill holes in the ceiling for where the lights would go, and cut holes in the ceiling to aid the rewiring. Another option could have been to lift the floor of the bedroom above, but the ceiling is already trashed from the fact there used to be a wall…
I also realised after removing the kitchen that the new kitchen, whilst very similar in layout, is not *quite* the same and this led to the need to move some switches and make adjustments. In particular the new oven is a range cooker with a double oven, it has a much higher potential power requirement than the old oven and the old wiring was simply not sufficient. I’m also brining a unit further out into what used to be dining room space (to accommodate the wider oven) and this would put a set of draws in front of a double socket. So the socket needs to be moved a few feet over. None of this is terribly difficult, however it is all work I need a qualified electrician to do, and that I need to pay for.
Gas safe engineer – The old and new ovens both have a gas hob. The old connection was fixed and needed a qualified gas engineer to disconnect it. He will need to come back to setup the right attachment for the new oven. This is another of those jobs which is really not very complicated, certainly no more so than regular plumbing. However when it comes to handling gas you must use a qualified engineer to do the work. In particular they have the tools to double check there are no gas leaks. As with the electrician, he will provide a signed document that I can use as proof that the work was done properly, which is key for insurance etc.
Plasterer – I’ve tried plastering, it is hard work, and hard to get right, plastering a ceiling is probably the last thing I would even contemplate trying myself. I need to have the ceiling plastered and make good the walls where the old dividing wall once was. With all the electrics tweaks, I’ll also need them to make good the various channels that need to be cut to accommodate wiring. And of course I ripped off old tiles. If I was going to tile again I could probably get away without re-plastering in those places, but I want to have just plain walls, so again require a plasterer to make good.
I’m also having the windows replaced by a window company, again in theory I could have tried to do this myself I guess, but it is not a job I fancy taking any chances on. Some of the value of the windows are the associated guarantee from being fitted by registered fitters. However this is sort of separate to the kitchen refit, it just happens to be something I’m doing around the same time.
So – when refitting a kitchen expect to have to do some electrical changes, particularly if upgrading an oven. And expect to need a plasterer to make things good again. If you have a gas applicance you will need a gas safe engineer.
But for everything else….there is me.
The main consideration I needed to make for removing the kitchen was hiring a skip sufficient to take away all the rubbish. This is quite tricky because it can be hard to visualise how much capacity you will need. On the one hand, all the cupboards disassemble into nice flat panels which pack nicely. On the other, its surprising how much space tiles take up when you’ve taken them off the wall. I filled 3 black bags. The oven itself takes up a chunk of space which doesn’t compress, the sink, the hob, the extractor etc. All things that needed room in the skip. I was also removing the carpet in the dining room, probably 15 square meters of carpet and the same again in underlay. It rolls up fairly tightly, but it is heavy and takes up space.
Ultimately I ordered a 4 yard skip, and it turned out to be pretty much perfect. I got everything in, and was able to take few things that my neighbour wanted rid of.
Other than that the issue was time, It took me a couple of days to disassemble most of the kitchen, and another to fill the skip and remove the last pieces once the gas hob was disconnected.
There was nothing that I found I couldn’t tackle on my own, so whilst things would go quicker with a helper, one wasn’t necessary.
One very useful thing I learned was the use of a wall paper stripper (steamer) to remove tile adhesive from the walls after the tiles come off. This was not at all obvious to me, initially I was going to try and use my oscillating multi-tool to cut away at it, but that wasn’t working very well and promised to be very slow going and dusty. I did a quick search and found that the adhesive will actually turn soft again under steam. This worked great, though I did blow the plaster in a couple of places by holding on too long, but since I knew I was re-plastering anyway, it was not a huge deal. It was pretty fast and left the wall pretty flat and undamaged by scraping (except for the aforementioned plaster blow outs which I could probably have avoided)
Next steps
I want to drill a hole for the extractor hood to vent to the outside. This requires a specialist tool, but it also requires me to be pretty sure where the extractor hood will be positioned I have the measurements from the kitchen plan, however I do need to allow for the walls to not be exactly vertical and it might push things over a little in the actual placement of units. The chimney of the extractor is 220 wide, the hole needs to be a minimum 125mm, so there is a little give, but it will require some careful double checking before I start to drill.
I am installing under floor heating, this will raise the floor heights, and the units will need to be commensurately higher, so some consideration for what I’m installing under the units to raise them or if they will have enough adjustment built in.
I was checking the documentation for the extractor hood and discovered that the minimum height it has to be installed above a gas hob is 700mm, which when combined with the minimum stated height of the extractor hood itself and the height of the floor/oven etc, led to the conclusion that my room is not tall enough…So I know I’m going to have to make some fairly aggressive alterations to the chimney sections to allow them to fit in a smaller space.
I still have to work out the details of the plumbing for the new sink and tap. It is highly likely that I’m going to have to shut off the mains water and substantially rework the pipes to fit the new requirements. But there is not much to do about that until the actual kitchen arrives to fit against.
Wren Kitchens wanted about £3000 to ‘fit the kitchen’ with all these considerations I’m not entirely clear whether that would have included absolutely everything that needed doing, or whether some things would have been considered optional extras (moving plug sockets?) In any case I’m on track to spend half of that, even including all the plastering that is more to do with the wall removal than the kitchen install.